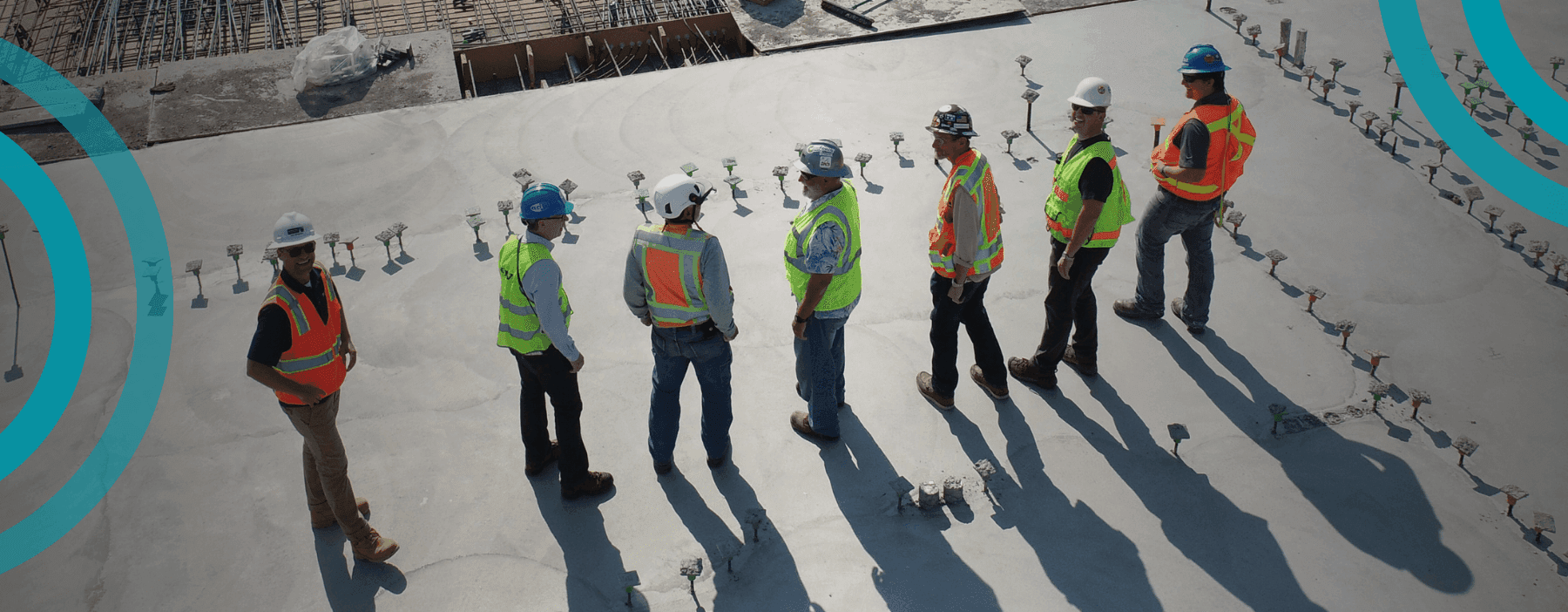
Hearing conservation - Understanding OSHA requirements
Search for articles by category
OSHA is a regulatory agency within the U.S. Department of Labor, responsible for setting and enforcing workplace health and safety standards. One of its critical focus areas is occupational noise exposure, to help protect against noise-induced hearing loss (NIHL).
Under the OSHA hearing protection standard, employers are required to implement a hearing conservation program if workers are exposed to noise levels at or above 85 decibels (dB) averaged over an 8-hour work shift.
Why should companies conduct audiometric testing?
Audiometric testing is a crucial component of workplace hearing conservation. It can help to identify early signs of hearing loss and ensures workers receive the necessary interventions before permanent damage occurs. OSHA’s audiometric testing requirements mandate that employers provide hearing tests to employees exposed to hazardous noise levels, ensuring compliance with workplace safety regulations.
The benefits of conducting audiometric tests include:
- Early hearing loss detection, possibly preventing long-term damage or mitigating the negative effects of long term noise exposure
- Active steps toward OSHA compliance, reducing the risk of regulatory fines and legal repercussions.
- Data-driven interventions, enabling employers to implement better noise control measures.
- Improved workplace safety, allowing employees to perform their duties without impaired hearing.
The key components of a hearing conservation program include:
1. Noise monitoring
Employers must measure and document noise levels in the workplace using specialized equipment like sound level meters or noise dosimeters. Sound levels from 80 to 130 dB need to be integrated into noise measurements.
Monitoring needs to be repeated whenever there’s a change in process, equipment or controls that might increase noise exposure to an extent that:
- Additional employees might be exposed at or above action level, or
- The attenuation provided by hearing protection is not adequate to meet OSHA requirements
Employers are also responsible to notify each employee exposed at or above an 8-hour time-weighted average (TWA) of 85 dB, of the results of the monitoring process..
2. Audiometric testing
OSHA requires employers to provide a baseline hearing test within 6 months of an employee's first exposure at or above the action level, and at least annually after obtaining the baseline audiogram.
Each employee's annual audiogram must be compared to their baseline audiogram to determine if the audiogram is valid and if a standard threshold shift has occurred.
Pure tone air conduction hearing threshold examinations need to include a minimum of 500, 1000, 2000, 3000, 4000, and 6000 Hz. In addition, tests at each frequency need to be taken separately for each ear.
3. Hearing Protection Devices (HPDs)
If the comparison of an employee’s annual audiogram indicates a standard threshold shift compared to their baseline results, the employee needs to be informed thereof within 21 days.
In cases where the annual audiogram shows a standard threshold shift, the employer may obtain a retest within 30 days, and consider the results of the retest, as the annual audiogram.
Unless a healthcare practitioner determines that the shift isn’t work-related or aggravated by occupational noise exposure, employers need to:
- Fit and train employees not using hearing protection on its use and care.
- Refit and retrain employees already using hearing protection - with greater attenuation if necessary.
- Refer employees for a clinical audiological evaluation if additional testing is required or you suspect a medical pathology is caused or aggravated by the use of hearing protection.
- Inform employees that an otological exam needs to be performed if you suspect a medical pathology, unrelated to the use of hearing protection.
If an employee’s exposure to noise is less than an 8-hour TWA of 90 dB, and a standard threshold shift is not persistent, you need to inform the employee of the new result findings and the employee can discontinue the use of hearing protection.
4. Employee training
Employers need to train each employee exposed at or above an 8-hour TWA of 85 dB, and ensure employee participation in the program.
Training needs to take place annually and must include information on:
- The impact of noise on hearing,
- The purpose, attenuation capabilities, use cases and care of hearing protection, and
- The purpose and process of audiometric testing.
5. Recordkeeping
Employers must maintain records of noise exposure monitoring for at least 2 years, and audiometric test results for the duration of an employee's employment.
What happens if companies violate OSHA noise exposure requirements?
Failure to comply with OSHA regulations can lead to severe consequences, including:
- Fines and penalties: OSHA can issue substantial fines for non-compliance, with penalties increasing for repeated violations.
- Employee health risks: Workers may suffer permanent hearing loss, leading to productivity losses and increased worker compensation claims.
- Legal liability: Companies may face lawsuits from employees affected by workplace hearing damage.
- Reputational damage: Non-compliance with OSHA hearing protection standards can harm a company's image and credibility.
Occupational hearing tests: The future of audiometry
Traditional hearing assessments required sound booths, making workplace hearing tests challenging in many settings. However, advancements in boothless audiometry allow for flexible, on-site hearing testing, to help support compliance with OSHA regulations.
Final thoughts
Protecting employees from noise-induced hearing loss is a fundamental responsibility of employers. By following OSHA hearing protection standards and implementing an effective hearing conservation program, businesses can safeguard worker health while avoiding regulatory penalties. With advancements in digital audiometry, conducting workplace hearing tests has never been more accessible.
If your company would like to enhance your hearing conservation efforts, investing in modern hearing test equipment is a proactive step toward compliance and long-term employee wellbeing.
Looking for an OSHA compliant hearing test solution? Reach out to our team today.
Email us or call
US: +1 (415) 825-3064 | RSA: +27 (0) 12 030-0268